again here the materials list from the first post:
For the Neck Forms:Bookboard (or 3ply Chipboard)Thin Headliner Foam
Fabric
Trim
Adhesive (one that can be used for adhering foam as well as paper and fabric)Boxcutters or Heavy Duty Shearsa Cylindrical Form (for molding)Steel for weighting the Form
For the Stand:Steel Tubing 3/8"All Thread Pipe (called a nipple in the hardware world)1/4"
Washers 5/16'Nuts 3/8"Finials that fit a 1/4" nippleAntique/Vintage Metal Lamp Bases
Spray Paint#6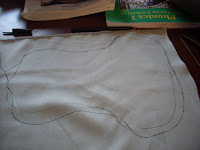
Trace the template onto the fabric side of the foam, allow 1/4" for the curve of the form. Cut out.
#7
Use a
sparing amount of glue I used "Fabri-Tac" brand, it has intense fumes (smells like nail polish remover due to it's high acetone content) so be outside or in a really well ventilated area.
It dries fast so I only apply a small amount, working from the
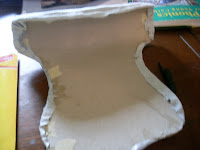
bottom/front to the top/back. That way if there are any areas that are cut short it'll be in the back. Also you can go back and use snippets to cover areas in the front that are exposed.
#8
Trace the Template twice on the backside of the fabric you are using. Make a 1/2" (allowance) larger outline around the templates. This allows you to fold the fabric over the edge to glue on the backside. Cut out the shapes. One of the pieces will be for the front and one for the back.
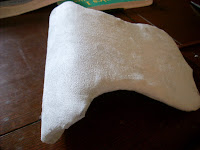
#9
If you have a curvy shape like mine you'll want to start gluing in the back so you can stretch or pull the fabric tight as you go. On the inside curves I cut small incisions (like tabs but not all the way to the inside line) so that I could wrap it w/o buckling the fabric. Start by applying the glue to the chipboard on the backside then drape the fabric (right-side facing you) over the foam covered form and press the edge of the fabric into the glue. Continue
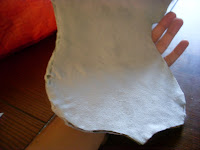
working your way down the form a little at a time tugging tight each time so you have a smooth surface.
As you work your way down be careful not to get excess glue from your fingers on the front of the fabric. (you can step away and wash the glue from your fingers frequently - this also allows the sections you're working on to dry a bit)#10
Flip over your form, now covered in fabric on the front.
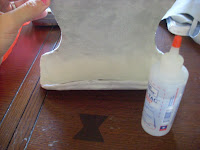
This time you might want to start gluing from the bottom up, due to the inside curve at the top. Take the second piece of fabric you cut and start gluing it on covering the fabric folded over from the front. If you cut the fabric without an allowance match up the edges of the form and the fabric. If you have an allowance apply the glue near the edge of the form but not all the way so you don't have glue dripping over to the front. Then you take the fabric an apply it not gluing the edge down if you have and allowance - it'll have a floppy edge that you'll trim with scissors later to
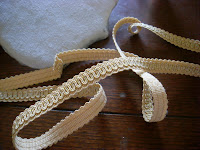
get a clean edge.
#11
Take your chosen trim and measure around the edge of the covered form before you start gluing. Or you can leave it uncut (like I do) and cut off the piece when you get back to the starting point.
Voila!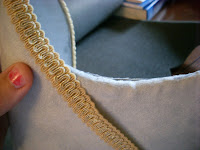
At this point you can use the forms for flat display
or you can continue on to build the stand.
Sorry about missing some of the photos. I forgot to take advantage of some picture opportunities. Maybe when I make my next batch I'll get some
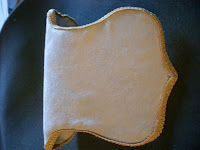
more.